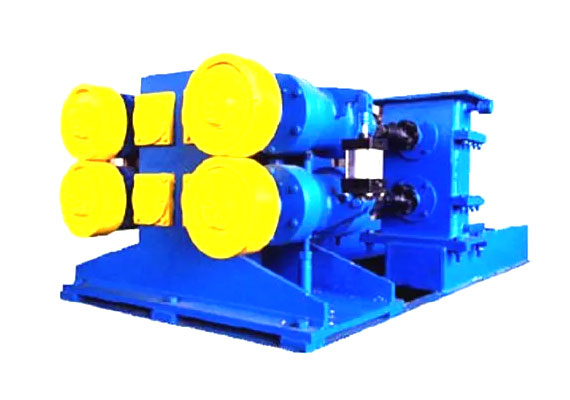
Tail Breaker
We are one among the prominent manufacturers and exporters of best quality Tail Breaker. The offered product has fetched high demands for its longer service life and resistance to abrasion. Attributing to its anti-corrosive properties and perfect finish, the whole range of high quality tail breakers offered by us has been a preferred choice of our revered clients.
Tail breaker is configured following the flying shear and before the cooling bed to decrease the velocity of TMT bars. It operates through AC and DC variable drives. The rolls are separated by a pneumatic cylinder. It includes a steel body, pneumatic cylinder, top and bottom arms and rolls.
We are a leading manufacturer of Tail Breaker that is made from high-quality raw material and advanced technology. Tail breaker offers excellent performance and durable nature. It is available at an economical price.
Features / Specification
- Housing will be of steel
- Pinion body steel fabricated
- Roll will be of EN-31
- Gear will be of forged steel EN-9 / 19 / 24.
- Anti friction Spherical Roller Bearing.
- Forged lubrication.
- Efficiently peak load worked design.
- Gear will be hardened & grinded for smooth run.
- Transparent & Heat dissipation window.
- Double oil seals to protect any leakage.
- Forged Steel EN-8 fully machined Shaft.
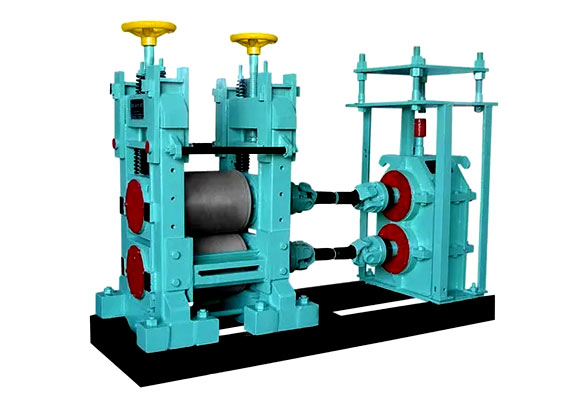
Pinch Roll
It is installed at various places in a rolling mill such as between the roughing mill and the intermediate mill, before and after the TMT Quenching Box to maintain the speed and tension of bars. It is driven through AC/DC Motor and consists of 2 Hi Gear Box, solid rolls with cardan shaft.
DC Pinch Rolls are installed at different places in a working rolling mill, including the place between roughing mill and intermediate mill as well as before and after TMT quenching box. The use of these rolls support maintenance of speeds and provide for consistent tension of bars
AC Pinch Rolls find application in pushing material in particular direction and are designed to deliver precision working, thus allowing movement of the material over a distance without making in them any physical changes.
Features / Specification
- DC Pinch Rolls are made available in two versions – conti-leaver type and pneumatic up to 360mm crs
- DC Pinch Rolls are made available in two versions – conti-leaver type and pneumatic up to 360mm crs
- We hold expertise in providing AC pinch roll comprising conti-leaver type mechanical up to 400mm crs
- Pinch rolls featuring use of sensors that allows precision breaking up of speed of hot flowing material
- Top roll comes raised pneumatically or lowered with bottom roll in adjustable finish
- Pinch roll housing comprising sturdy welded construction
- Pinch rolls feature wear resistant surface with anti friction bearing mounting support
- Pneumatic cylinder for raising /lowering upper rocker arm
- Spindle provided for meeting the needs of adjustment of bottom pinch rolls
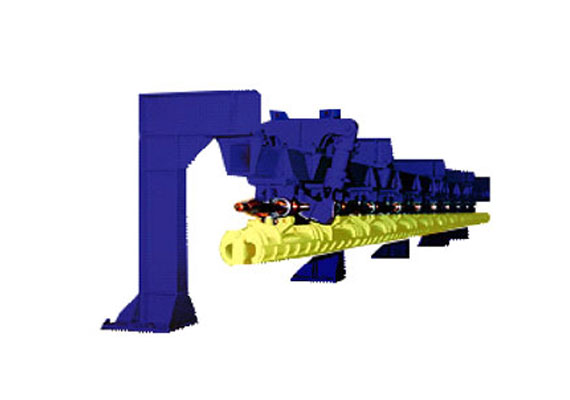
Twin Channel
Our company is engaged in offering high grade Twin Channel Machine that is widely installed along the side of the entry of the cooling bed. The twin channels consist of alternatively opening flaps through a hydraulic cylinder and CAM system. In this, the bar enters the closed flap that opens when the full bar has been obtained. It has a free fall on the straightening pockets of the rake type cooling bed, which moves on the fixed & moving rakes to the mill run out table.
This is an excellent system as it carries the bar in a closed channel, minimizing the accident hazards. Specifically while carrying out high speed rolling the system is an absolute necessity.
Its design features makes it possible to work in conjunction with braking pinch rolls, minimizing the length of run-in. The operations of twin channel are automated and are guided by the discharge of the rods from dividing shear. An innovative idea for cast iron center boxes has drastically brought down maintenance time.
Features / Specification
There are ample of features and advantages that make our twin channels the most advanced one in the entire industry. Some of the striking features embarked with our manufactured TWIN Channels are as following:
- Twin water-cooled C-type channels with water cooling arrangement
- Supporting arrangement for the twin-channel and drive system
- Cam device for opening closing of the pipes
- Hydraulic Drive for operation of the cams
- Prevention from warping
- Highest level of safety
- Closed channel for transferring bars
- Can be attached to braking pinch rolls
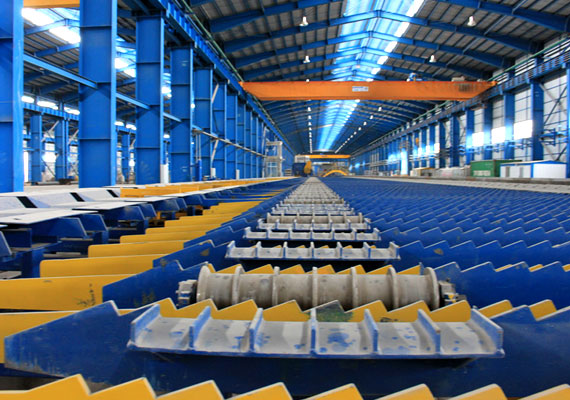
Cooling Bed
Full mechanical component standardization of our cooling bed assures constant equipment quality, as well as high performance levels. Depending on differing speed requirements, cooling beds’ entry can be completed with lifting aprons and natural braking, magnetic braking, or twin channel and mechanical braking. For special applications, the cooling beds are provided with slow cooling by insulated covers and forced cooling by water spray systems or water tanks. A twin or double twin channel system for extremely high rolling speeds is available.
These are the types of Cooling Bed we provide :
- Automatic rake type cooling bed which transfers the material by one pitch for every rake movement. These are provided with twin channel bar delivery system or run in table with apron type diverters. The bed is provided with bar alignment.
- Turn over type cooling bed for alloy steel which rotates the bars by one revolution every time the rake moves by a pitch. These impart superior straightness in material improvised metallurgical properties as the bars are uniformly cooled.
Features / Specification
- We hold expertise in providing cooling beds from 9.5mtr up to 66mtr
- These can also be developed as per customer’s requirement
- We have with us rich industry experience of commissioning more than 10 automatic beds throughout India
- The use of cooling bed of rack design is for providing uniform air-cooling to TMT bars
- It also helps in transporting in phased manner from entry of cooling bed to the discharge side.
- Front end of bars leveled at discharge side with fixed number of bars provided for final length cutting through cold shear as well as bundling process
- Superior working mechanism of the bed ensures bars are positioned uniformly over toothed racks
- Cooling bed designed keeping in consideration smallest and maximum size of bars that need to be rolled from finishing mill stand as well as cooling time needed for different sizes of bars
- Straightening racks comprising cast iron toothed blocks that assist in receiving bars and straightening it at temperature of around 600oC
- Movable rack mechanism to move in x and y axis which will be profile cut to suit smallest size as well as maximum bar size
- Fixed rack mechanism that receives bars from movable rack mechanism as bars are being transferred toward delivery side of cooling beds
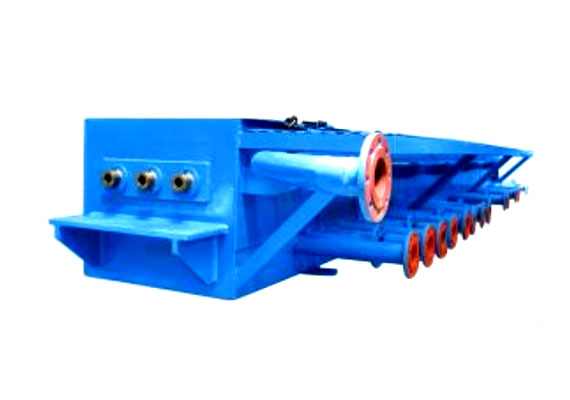
TMT Quenching Box
We are a credible name that is involved in the manufacturing and exporting of invincible quality TMT Quenching Box. Known for their non-corrosive properties and excellent finish, these are widely applauded among the customers we have. Driven by a client-centric approach, we make the offered equipment in accordance with the industry set standards.
Features / Specification
- Our offered TMT system is of multiple injector type, high grade quenching boxes that clean the surface through the process of scrubbing.
- The process begins by positioning the motorized valve and fitting the opening of the nozzles.
- The quenching box allows the multiple entry of fresh water at regular time duration that saves the time of quenching process.
- These assist in enhancing the strength of steel to provide best possible Thermo Mechanical Treatment (TMT) that assists in enhancing corrosion resistance as well as mechanical properties including Bending, Tensile strength, Yield Stress, Elongation etc.
- Our designed quenching box has consistency of tensile strength, ability to cut bars accurately.
- Fabrication through CNC profile Cutting Machines and welding machines
- IS 304 grade stainless steel casting done through investment casting technique
- In-house gear grinding and testing facilities to ensure the highest standards in manufacturing of shears and pinch rolls
- Experienced team of engineers and fitters dedicated to the manufacture of the quenching systems